Pressure sensors can be designed to withstand harsh environments including high temperatures and corrosive atmospheres. Here are some ways this can be achieved:
Material Selection: Pressure sensors designed for harsh environments require meticulous material selection. Stainless steel, renowned for its exceptional corrosion resistance and mechanical strength, is a staple choice for sensor construction. Its various grades offer specific advantages, such as improved resistance to pitting corrosion or high-temperature applications. Titanium, prized for its remarkable strength-to-weight ratio and resistance to corrosion, finds extensive use in aerospace, chemical processing, and marine industries. Its compatibility with aggressive chemicals and elevated temperatures makes it an ideal candidate for demanding environments. Furthermore, advanced engineering plastics like PEEK exhibit outstanding chemical resistance, high mechanical strength, and exceptional thermal stability, making them suitable for applications where metal sensors may falter. These materials undergo rigorous testing to ensure compliance with industry standards and performance expectations in harsh conditions.
Sealing: The sealing of pressure sensors is paramount to safeguard sensitive internal components against harsh environmental conditions. Various techniques are employed, ranging from laser welding and fusion bonding to hermetic sealing processes. Laser welding creates a robust, leak-proof seal by melting and fusing materials together, ensuring the integrity of the sensor's enclosure. Fusion bonding, on the other hand, utilizes adhesive bonding techniques to securely join components, offering excellent resistance to moisture ingress and corrosion. Hermetic sealing involves creating an airtight seal between materials, typically using soldering or brazing methods, to prevent the penetration of gases and liquids into the sensor's interior. These sealing methods undergo stringent quality control measures to verify their effectiveness and reliability under extreme conditions.
Coatings: Pressure sensors may feature specialized coatings to enhance their resistance to corrosion, abrasion, and chemical exposure. These coatings, applied using advanced deposition techniques such as physical vapor deposition (PVD) or chemical vapor deposition (CVD), form a protective barrier on the sensor's surface. PTFE (polytetrafluoroethylene) coatings offer exceptional chemical inertness, low friction, and high temperature resistance, making them ideal for harsh environments where corrosive fluids or gases are present. Other coatings, such as ceramic or polymer-based coatings, provide additional protection against abrasion and wear, prolonging the sensor's lifespan in demanding applications. Coating thickness, adhesion strength, and compatibility with the sensor's materials are carefully optimized to ensure maximum performance and durability.
Isolation: In applications where direct exposure to harsh environments is inevitable, pressure sensors employ isolation techniques to protect sensitive components while maintaining accurate pressure measurements. This isolation can be achieved through the use of diaphragms, membranes, or fluid-filled systems. Diaphragms act as a physical barrier between the process media and the sensor's internal components, deflecting pressure fluctuations while transmitting the pressure signal to the sensing element. Membrane-sealed sensors feature a thin, flexible membrane that separates the sensing element from the process media, allowing for reliable pressure measurement without direct contact with corrosive fluids or high temperatures. Fluid-filled systems utilize a hydraulic fluid or oil-filled capillary tube to transmit pressure from the measurement point to the sensor, isolating it from harsh environmental conditions. These isolation methods are meticulously engineered to ensure accurate and reliable performance in challenging operating environments.
SPB8303CNG pressure transmitter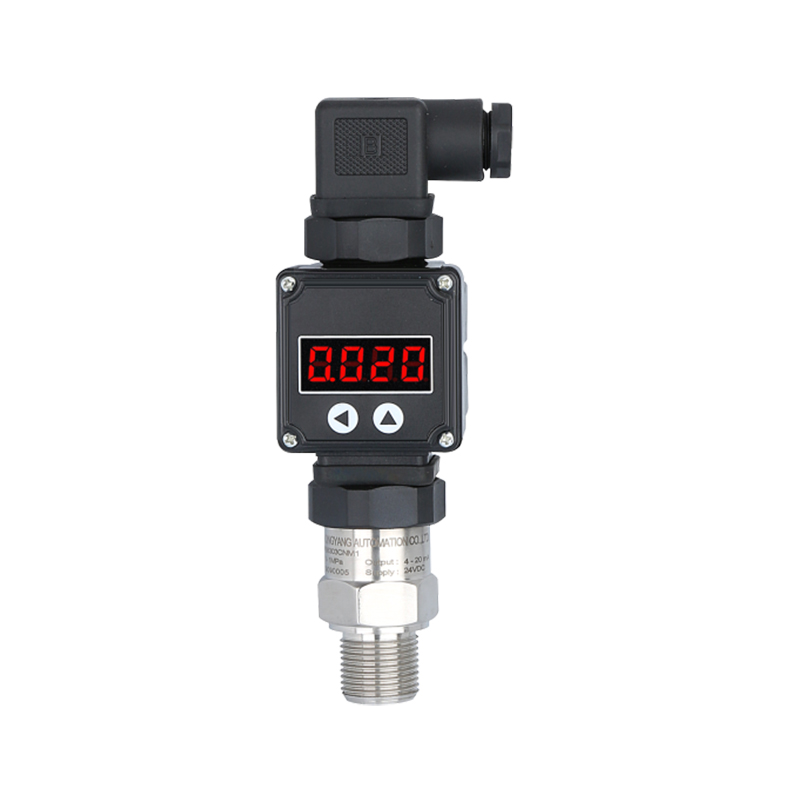