Temperature: Temperature fluctuations pose multifaceted challenges to liquid level transmitters. At elevated temperatures, materials comprising the transmitter can undergo thermal expansion, altering their physical dimensions and mechanical properties. This phenomenon extends beyond mere expansion; it can induce stresses within the materials, potentially leading to microstructural changes or deformation. Seals, diaphragms, and electronic components are particularly susceptible, as their performance may degrade under thermal stress. For instance, elastomeric seals may lose their resilience, compromising their ability to maintain a tight seal, while electronic components may experience changes in conductivity or performance characteristics. Moreover, temperature differentials across components can induce thermal gradients, exacerbating these effects and introducing additional sources of error. Conversely, low temperatures can induce contraction in materials, potentially impeding the mobility of moving parts or causing seals to stiffen and lose their flexibility. Thermal cycling, prevalent in applications subject to rapid temperature changes or operating in extreme environments, exacerbates these challenges by subjecting materials to alternating stresses, accelerating fatigue, and potentially leading to premature failure.
Pressure: Pressure variations represent a formidable challenge for liquid level transmitters, particularly in applications characterized by high-pressure environments or significant pressure differentials. In such conditions, transmitter components are subjected to mechanical stresses that can exceed their yield strength, leading to deformation, plastic deformation, or even catastrophic failure. For instance, diaphragms, commonly employed in pressure-sensitive transmitters, may experience excessive deflection or rupture under high pressures, compromising their ability to provide accurate measurements. Similarly, structural components such as housings, flanges, or mounting brackets may experience deformation or fatigue cracking if not adequately designed to withstand the applied pressures. Pressure differentials across the sensing element can introduce measurement errors, particularly in differential pressure-based transmitters, necessitating compensation algorithms to account for these effects. Variations in process pressure can impact the density and compressibility of the process fluid, altering its hydrostatic head and complicating level measurement calculations. Selecting pressure-rated components and employing robust design practices are essential for ensuring the reliability and accuracy of liquid level measurements in high-pressure environments.
Chemical Composition: Chemical compatibility is a paramount consideration in the design and operation of liquid level transmitters, especially in applications involving aggressive or corrosive fluids. Exposure to such fluids can trigger a cascade of deleterious effects, ranging from material degradation to catastrophic failure. Corrosive chemicals can attack the structural integrity of transmitter components, causing pitting, cracking, or embrittlement. For instance, metallic components may undergo chemical reactions, leading to corrosion or galvanic corrosion if exposed to dissimilar metals or electrolytes. Non-metallic materials such as polymers or elastomers may degrade under chemical exposure, losing their mechanical properties or undergoing chemical swelling. Abrasive fluids, containing suspended solids or particulate matter, can exacerbate wear on moving parts or sensor elements, accelerating mechanical fatigue and compromising measurement accuracy. Viscous fluids present their own set of challenges, impeding the mobility of moving parts or hindering fluid flow within the transmitter, thereby affecting response time and dynamic performance.
PB83 threaded full flat diaphragm 2
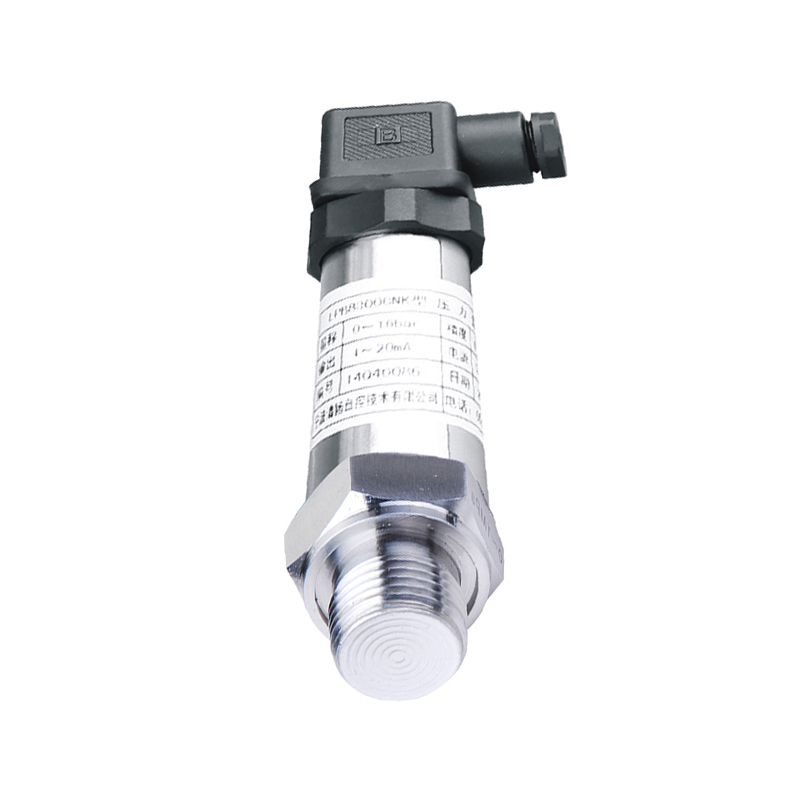