1. Sensor drift: Over time, RTD sensors can exhibit drift, where their resistance changes gradually, leading to inaccurate temperature measurements.
2. Mechanical damage: Physical damage to the sensor element or its connection points can occur during installation, handling, or operation, leading to erroneous readings or complete failure.
3. Contamination: Exposure to contaminants such as dust, moisture, chemicals, or oils can degrade the sensor's performance and accuracy.
4. Lead wire damage: Damage or degradation of the lead wires connecting the RTD sensor to the measurement instrument can lead to increased lead resistance, affecting the accuracy of temperature measurements.
5. Vibration and shock: High levels of vibration or mechanical shock, especially in industrial environments, can cause strain on the sensor element or lead wires, leading to damage or failure.
To detect and prevent these failure modes:
1. Regular calibration: Establish a comprehensive calibration program that includes detailed procedures for calibration, verification, and documentation. Develop a calibration schedule based on factors such as sensor usage, environmental conditions, and industry regulations. Utilize traceable calibration standards and certified calibration laboratories to ensure the accuracy and reliability of calibration results. Document all calibration activities, including calibration dates, results, adjustments made, and personnel involved, to maintain a complete calibration history and traceability.
2. Visual inspection: Conduct thorough visual inspections of RTD sensors using magnification tools and inspection checklists to identify even minor signs of damage or wear. Inspect the sensor element for microscopic cracks, scratches, or irregularities that may affect its structural integrity or electrical conductivity. Examine the lead wires and connection points under proper lighting conditions to detect corrosion, abrasion, or solder joint defects. Implement standardized inspection procedures and criteria to ensure consistency and reliability across inspection activities.
3. Environmental protection: Perform a comprehensive environmental assessment to identify potential sources of contamination, degradation, or stress that may impact RTD sensor performance. Develop customized environmental protection strategies based on the specific requirements and challenges of the application, considering factors such as temperature extremes, humidity levels, chemical exposure, and mechanical vibrations. Employ advanced materials, coatings, encapsulation techniques, and sealing methods to create robust barriers against environmental hazards while maintaining sensor accessibility and functionality.
4. Vibration isolation: Conduct detailed vibration analysis and modeling to quantify vibration levels and frequencies within the installation environment accurately. Utilize advanced vibration isolation techniques, such as modal analysis, finite element analysis (FEA), and vibration testing, to identify critical resonant frequencies and design effective isolation solutions. Select vibration-resistant materials, damping materials, and isolation mounts tailored to the specific vibration profile and dynamic characteristics of the equipment or structure. Integrate vibration monitoring and predictive maintenance systems to continuously assess vibration levels and optimize isolation effectiveness over time.
5. Temperature monitoring: Implement a comprehensive temperature monitoring system featuring advanced sensors, data acquisition systems, and analytical tools to ensure real-time visibility and control over temperature conditions. Deploy redundant temperature sensors and multi-point monitoring arrays to capture temperature variations across critical locations and detect potential hot spots or thermal anomalies. Integrate temperature monitoring with automated control systems, alarm systems, and remote monitoring platforms to enable proactive temperature management and rapid response to temperature excursions. Establish robust data logging and analysis procedures to track temperature trends, identify patterns, and optimize temperature control strategies for enhanced efficiency and reliability.
With bellows
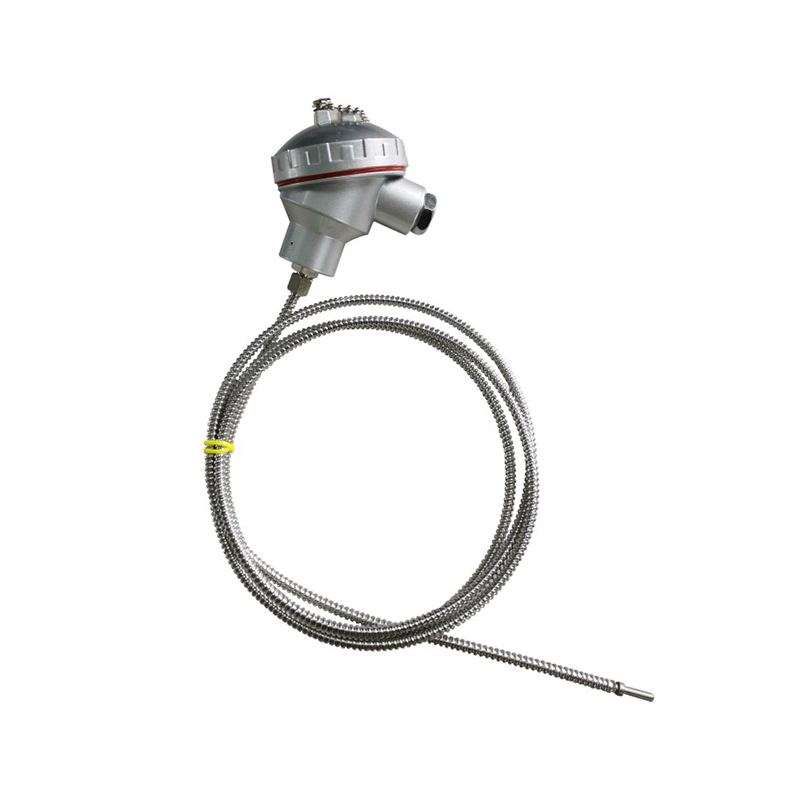